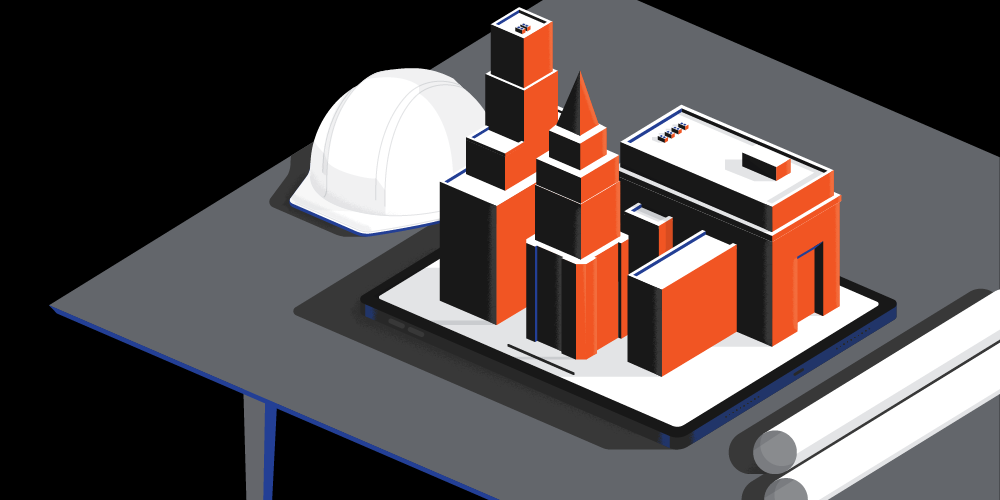
In today’s competitive construction and development landscape, delivering projects on budget without sacrificing quality has become more challenging than ever. This is where Value Engineering emerges as a critical methodology that can make the difference between a project’s success or failure.
What is Value Engineering?
Value Engineering is the systematic process of analyzing a project’s functions to identify and eliminate unnecessary costs while maintaining or improving performance, reliability, quality, and safety. It’s not simply about cost-cutting—it’s about maximizing value through the optimal balance of function and cost.
The key principle is achieving savings without quality compromise, something that is eminently achievable in the complex development business. Value Engineering examines materials, processes, and products to offer alternatives that deliver the same or better performance at reduced costs.
A Practical Example: Post-Tensioned Concrete Systems
One clear example of Value Engineering in action is the use of post-tensioned concrete systems versus traditional reinforced concrete. This alternative approach offers multiple advantages:
- Reduced thickness of concrete slabs
- Fewer beams required
- Lower quantities of reinforcement
- Smaller column and foundation sizes
- Better crack control
- Greater flexibility in planning and design
- Accelerated construction program
The cumulative effect of these improvements can lead to significant cost savings while maintaining or even enhancing structural performance.
Structured Process for Implementing Value Engineering
Successful Value Engineering doesn’t happen by accident—it requires a structured approach. Here’s a proven four-phase methodology that delivers results:
Phase 1: Information Gathering
- Assemble the Value Engineering Team
- Include designers, engineers, constructors, cost consultants, and end-users
- Establish clear roles and responsibilities
- Define Project Objectives
- Identify primary and secondary functions
- Establish performance requirements
- Determine budget constraints
- Clarify non-negotiable elements
- Collect Project Information
- Gather all design documentation
- Review specifications and standards
- Analyze cost estimates and breakdowns
- Identify high-cost areas
Phase 2: Analysis & Innovation
- Functional Analysis
- Break down the project into functional components
- Assign costs to each function
- Calculate value ratio (function ÷ cost)
- Identify low-value components with high improvement potential
- Creative Brainstorming
- Conduct structured workshops
- Apply divergent thinking techniques
- Generate alternative solutions
- Document all ideas without immediate evaluation
- Preliminary Evaluation
- Screen ideas against project constraints
- Identify promising alternatives
- Prioritize options based on potential impact
Phase 3: Development & Recommendation
- Detailed Analysis
- Develop technical details for each viable alternative
- Calculate life-cycle costs
- Assess implementation considerations
- Evaluate risks and dependencies
- Cost-Benefit Analysis
- Quantify savings for each alternative
- Identify qualitative benefits
- Calculate return on investment
- Compare alternatives objectively
- Recommendation Package
- Prepare detailed documentation
- Include technical specifications
- Provide clear cost comparisons
- Present lifecycle implications
Phase 4: Implementation & Feedback (Varies by Project)
- Decision Making
- Present findings to key stakeholders
- Address concerns and questions
- Secure approvals for implementation
- Document decisions for future reference
- Integration into Project
- Update design documentation
- Revise specifications and drawings
- Adjust project schedule
- Communicate changes to all stakeholders
- Monitoring & Feedback
- Track implementation progress
- Verify achieved savings
- Document lessons learned
- Establish feedback loop for continuous improvement
Real-World Case Studies: Is Value Engineering Worth It?
The simple answer is yes, but let’s look at the evidence through real-world examples:
Case Study 1: Commercial Office Tower – Sydney CBD
A developer was planning a 22-story commercial office tower in Sydney’s CBD with an initial budget of $210 million. The preliminary design featured a traditional reinforced concrete structure.
Value Engineering Approach:
- Reviewed structural system and proposed post-tensioned concrete slabs
- Redesigned the curtain wall system while maintaining aesthetic intent
- Optimized HVAC system specifications and zoning
- Reassessed fire protection systems against code requirements versus over-engineering
Results:
- Reduced floor-to-floor height by 100mm, saving on façade materials and vertical transportation costs
- Decreased overall concrete volume by 18%
- Reduced steel reinforcement quantities by 22%
- Maintained design intent and performance specifications
- Total savings: $17.5 million (8.3% of project cost)
- Additional benefit: 3-week reduction in construction schedule
Case Study 2: Healthcare Facility – Melbourne
A regional healthcare provider was expanding their facilities with a new 15,000 sqm medical center. Initial cost estimates exceeded their budget by $12 million.
Value Engineering Approach:
- Analyzed space planning and clinical workflow
- Reviewed mechanical and electrical systems
- Evaluated finishing materials and fixtures
- Assessed construction methodologies
Results:
- Reconfigured layout to reduce circulation space by 8% while improving workflow
- Standardized room sizes and layouts for repeatability and efficiency
- Implemented modular construction for bathroom pods
- Utilized more efficient mechanical systems with zoned controls
- Substituted specified flooring materials with alternatives meeting same infection control standards
- Total savings: $15.3 million
- Additional benefits: 15% reduction in operational energy costs, improved maintainability
Keys to Success in Value Engineering
For those considering implementing Value Engineering on their next project, these factors are critical to success:
- Early implementation: Ideally during concept or schematic design phases
- Multidisciplinary involvement: Engage all relevant stakeholders and experts
- Client/end-user participation: Ensure their needs remain the priority
- Function-focused approach: Concentrate on what elements do, not just what they are
- Open-minded evaluation: Be willing to challenge conventional solutions
- Comprehensive assessment: Consider both quantitative and qualitative factors
- Clear communication: Document and explain all recommendations thoroughly
Conclusion: The True Value of Engineering
Value Engineering is not merely a cost-cutting exercise—it’s about delivering maximum value by optimizing the relationship between function and cost. When implemented properly, it can yield substantial savings without compromising quality or performance. In fact, many Value Engineering solutions actually enhance project outcomes while reducing costs.
We were directly involved with a project in Brookvale, NSW. The original engineering solution proposed grout-injected piles for the substructure. After careful analysis, we identified high-level footings as a viable alternative. This single Value Engineering decision presented a saving to the developer of approximately $200,000 without compromising structural integrity or performance.
In the increasingly complex world of development and construction, Value Engineering provides a structured methodology to achieve more with less. All it takes is experience, a trained eye, and an impartial view.
For developers, contractors, and project managers facing budget challenges, the question shouldn’t be whether Value Engineering is worth it, but rather how quickly it can be implemented to start realizing its benefits.